Erfolgs-
geschichte
Dynamische Lagerplatzzuweisung: Die Artikel stets auf dem besten Platz!
Dynamische Lagerplatzzuweisung: Die Artikel stets auf dem besten Platz!
Die Firma CLAAS in Harsewinkel produziert in ihrer modular aufgebauten Hauptmontagelinie Mähdrescher mit einer hohen Variantenvielfalt. Auch die weiteren Montagelinien mit dem Selbstfahrenden Feldhäcksler und dem Systemtraktor sind auf eine hohe Varianz und kundenspezifische Anforderungen ausgelegt. Für die Anstellung der großen Materialvielfalt wird daher eine große Menge der Materialbedarfe in der zentralen Kommissionierung auftragsspezifisch zusammen- und bereitgestellt. Diese Aufträge werden in 13 Kommissioniergassen für über 70 Produktionsversorgungsbereiche zusammengestellt. Die Struktur der Lagerbereiche in den jeweiligen Gassen ist dabei einheitlich und gleich definiert, wobei die Anzahl der zugeordneten Materialien und die Anzahl der Produktionsversorgungsbereiche (PVB’s) sehr unterschiedlich ist. Dadurch kommt es in den jeweiligen Kommissioniergassen zu sehr unterschiedlichen Pickaufwänden und Auslastungen.
In der zentralen Kommissionierung arbeiten die Mitarbeitenden in einer schichtweise fest zugewiesenen Gasse. Durch die statische Größe der Lagerbereiche und den unterschiedlichen Stellplatzbedarfen der PVB’s, kommt es durch die heutige Ausweichstrategie und Lagerbereichssuche jedoch ggf. zu langen Fahrwegen und somit zu hohen Kommissionieraufwänden für einzelne Mitarbeitende.
Um Lastspitzen zu vermeiden, wird unregelmäßig ein sog. „Pick-Puzzle“ gelöst und Artikel werden in Gassen verteilt. Diese Aufwandsschätzung soll mit einem kurz- bis mittelfristigem Planungshorizont im Hinblick auf das Produktionsprogramm optimiert werden. Datenbasiert soll eine bessere Einlagerungsstrategie abgeleitet werden, die im Hinblick auf die bestehenden Auslagerungen (basierend auf dem aktuellen Produktionsprogramm) optimiert wird. Als Resultat sollen die Wege und schlussendlich die Auftragszeiten durch eine bessere Lagerplatzvergabe reduziert werden.
Der Lösungsansatz beinhaltet drei Schritte:
1) Basierend auf dem Bauprogramm der kommenden Wochen und Monate wird ein Bedarfs-Forecast im SAP erstellt.
2) In einem repräsentativen Zeitraum wurden Daten über die Pick-Prozesse mit Hilfe von Motion-Mining® aufgezeichnet. Aus diesen Daten wird eine Schätzung von Aufwänden je Pick und Wegzeiten je Lagerplatz abgeleitet und bewertet.
3) Aus der Kombination der beiden Datenquellen können Erkenntnisse für den Personaleinsatz, sowie die Einlagerung von Artikeln abgeleitet werden, um die Auftragszeiten zu reduzieren.
Im Ziel der Umsetzung steht ein verbesserter Personaleinsatz. Sie bietet bessere Lagerplatzzuordnung der Materialien zur Effizienzsteigerung des Kommissionierprozesses, eine bessere Personaleinsatzplanung und damit verbunden eine bessere Auslastung der Mitarbeitenden in der Kommissionierung und weniger Aufwand & Kosten je Pick-Vermeidung von unnötigen Wegen.
Für die Umsetzung wurden Methoden und Instrumente wie die Auswertung von SAP-Daten über Bedarfe und Kommissionieraufwände, eine Prozessanalyse mittels Motion-Mining® unter
Berücksichtigung der einzelnen Pickdaten, ein Tableau-Dashboard zur Personaleinsatzplanung
mittels Bedarfsprognose und Workshops zur Einlagerstrategie.
Das sagen die Leuchtturmfabriken zu den Erfolgen:
Die dynamische Zuweisung der Lagerbereiche bietet uns eine gute Möglichkeit, den für CLAAS effizientesten Weg zu gewährleisten, um die Materialien gebündelt für eine optimierte auftragsspezifische Kommissionierung anzuordnen. Dadurch werden nicht nur unnötige Wege vermieden und die Mitarbeiterauslastung reduziert, sondern auch eine ganzheitliche Glättung der Aufwände über alle Kommissioniergassen hinweg sichergestellt.
Unsere Mitarbeitenden sollen durch die dynamische Einlagerung der Kommissionierbedarfe, verkürzten Wegzeiten (hoher Anteil am Kommissionierprozess) ausgesetzt sein. Hierfür wurde mit den MotionMiners, dem Projektteam, den Mitarbeitenden sowie dem Teamsprecher des Bereiches eine dreiwöchige Prozessaufnahme und –analyse in enger Zusammenarbeit durchgeführt.
Neben der Optimierung innerhalb einer Gasse, kann die Auslastung über alle Gassen hinweg homogener verteilt werden. Durch die differenzierte Auslastung gab es “unbeliebte Gassen” unter den Mitarbeitern welche einen höheren Arbeitsaufwand als andere Gassen beinhalten. Die bisher manuell gestaltete Planung der einzelnen Gassen mit einem hohen Initialaufwand und der Betrachtung diverser Restrektionen, kann durch die Optimierung einfacher und effizienter umgesetzt werden.
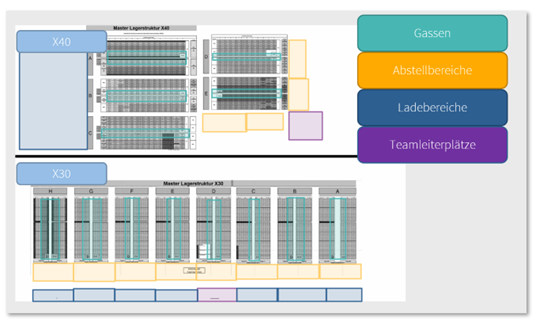